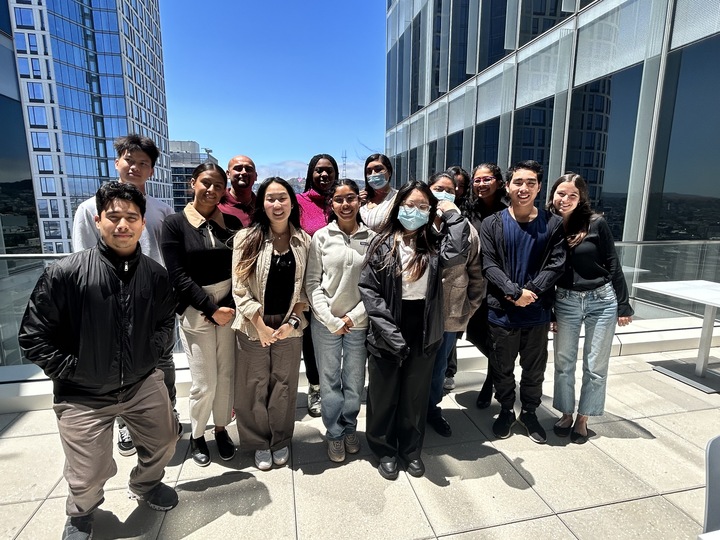
Giving back is a full-time passion for the STO Building Group network of companies. One of the ways BCCI Construction has fostered its relationship with the San Francisco community is by partnering with a local foundation that helps students discover their own passions in the real estate and AEC industries.
The Presidio Bay Foundation is a 501(c)(3) non-profit focused on empowering underserved youth through educational and career opportunities in commercial real estate. Their mission, alongside BCCI’s commitment, is to forge pathways for youth to become future leaders in shaping more equitable neighborhoods and cities by providing resources to pursue careers in real estate, architecture, engineering, and construction. Each summer, the program hosts a cohort of students who engage in an intensive 10-week curriculum that exposes them to various facets of commercial real estate, including finance, design, management, city planning, development, sustainability, and retail. Beyond education, each student has the unique opportunity to network with industry professionals and mentors. Excitingly, the foundation will soon be launching a workforce ready initiative to assist young adults in having direct access to additional internships and entry-level roles.
According to Mallory Wall, vice president of client services at BCCI, Presidio Bay prioritizes community building by supporting cultural, racial, and gender diversity and providing Scholars with comprehensive training and connections for future success. Wall has volunteered as a construction mentor for the program for the last three years and says their unique approach to fostering new generations of leaders sets them apart from other, similar programs.
“It brings me so much joy seeing the students in the program really wanting to learn and understand how real estate development works,” she says. “Presidio Bay is genuine and passionate about instilling confidence and creating a launching pad for students to have a voice in shaping the future of their communities.”
“Whether it’s giving these young people the confidence to speak or sparking curiosity to seek a future career path in the industry, if you just touch one person, that’s what matters.”
Mallory Wall, Vice President, Client Services
The students agree. “Even if you don’t come from a background with exposure to the real estate industry, you feel embraced, encouraged, and empowered for the future,” says one recent participant. “The way this program is structured, it’s like the difference between receiving a handshake and a hug.”
Since 2021, the program has graduated 32 students and invested over $280,000 in scholarships and program growth. Looking ahead, the Presidio Bay Foundation aspires to expand its influence across the Bay Area and, ultimately, the US. And while these ambitions will undoubtedly make a tremendous impact on the future of commercial real estate, Wall knows that the local, individual interactions within the program are the ones that truly make the biggest difference.
WATCH: DEVELOPING OUR FUTURE
Hear from students and see the Presidio Bay Foundation’s impact in action in this short documentary. You can also learn more about their accomplishments in their annual report on pbvscholarship.com.
Originally Published in STOBG Insights Issue 1 2024.
Building green isn’t just a trend—it’s a responsibility. In 2021, several STOBG companies signed on to the Contractor’s Commitment, a pledge created by contractors for contractors, to set sustainability targets and measure their progress—divided into Good, Better, or Best tiers. Over the last two years, those early signatories were able to provide valuable input to make the Commitment even stronger and more impactful.
“Being one of the early signatories for the Contractor’s Commitment has been so critical for BCCI,” says BCCI Construction senior director of marketing, Cynthia Gage. “You’re in the room with a project team and you’re able to have real-life, on-the-ground conversations about sustainability and what makes a difference in construction.”
By pledging to the Contractor’s Commitment, BCCI, Ajax Building Company, Abbott Construction Los Angeles, and Structure Tone New York joined a larger movement to impact the sustainability of building projects and inspired others, including subcontractors and clients, to follow suit.
“We initially proposed the Contractor’s Commitment to Structure Tone New York because New York’s best practices were in most alignment with what it entails,” says Jennifer Taranto, STO Building Group vice president of sustainability. “We received plenty of support from our president, Mike Neary, and we saw that this would be meaningful for our clients.”
Two years into the Commitment, and the STOBG teams have seen progress and efficiencies in several facets of construction.
WASTE DIVERSION
Waste diversion is one area where all four STOBG companies report clear success. “Many of the goals at the Good tier, including waste management, are already what we require of our projects,” says Teresa Fait, project manager at Abbott Construction in Los Angeles. “The Commitment gives us added framework for educating and tracking.”
Similarly, BCCI was already complying with California’s stringent sustainability requirements, and they were empowered by the Contractor’s Commitment to take things a step further and build more waste management tactics into each stage of a project. According to Priyanka Jinsiwale, project manager of sustainability and ESG at BCCI, the company is committed to standardizing waste diversion practices on all of their projects.
“Ensuring early engagement is conducted on all projects and integrated into our project workflow is key since these metrics need to be tracked consistently. We’ve created several implementation tools and templates to help.”
Priyanka Jinsiwale, Project Manager, Sustainability & ESG
Structure Tone NY uses on-site source separation methods for select waste streams to increase the landfill diversion rate, rather than commingling all of the discarded materials in a single dumpster. “Although there are space limitations on our jobsites, we’ve found tremendous success with our closed-loop gypsum recycling efforts,” says Ryan Hughes, Structure Tone NY sustainability manager.
Local wallboard manufacturers such as USG and CertainTeed/Saint-Gobain take back the site-separated drywall trim scrap and use it as feedstock to create new products. “We’re also separating wood and metal on select projects and working with partners to recycle our carpet scraps as another way to contribute to the circular economy,” Hughes adds. By salvaging, donating, and reusing existing materials even before demolition, the Structure Tone team was able to achieve the Commitment’s Better tier. NYC also has the benefit of using Cooper Recycling, a nearby materials recovery facility with an RCI-certification that demonstrates best-in-class sorting practices.
CARBON TRACKING
Although carbon tracking was not a new task for Ajax, applying an anti-idling practice on all sites was a recent change for the company. Ajax’s anti-idling policy mandates that all engines—from passenger vehicles to construction equipment—must be turned off when not in use.
“Some people had a habit of getting out of their truck and running into the trailer for a meeting while the truck’s still running,” says Rowdy Francis, Ajax quality manager. “We’ve now addressed that. It’s a small thing but it reminds everyone to be more cognizant.”
BCCI also took their efforts on carbon tracking up a level since signing the Commitment. The team proactively began analyzing their baseline and identified areas of improvement. “Although 30% of our projects are required to be tracked under the guidelines of the Contractor’s Commitment, BCCI is aiming to track 80% of our projects,” says Jiniswale. As a new service offering, Structure Tone NY has also begun to track embodied carbon for projects seeking to measure their environmental impacts associated with materials and worker commutes.
UTILITY USAGE
Structure Tone has implemented various measures to monitor and reduce their utility consumption, but tracking and documenting those efforts at first posed a challenge. The team has since found an innovative solution to help, says Hughes. WASHBOX monitors temporary water use on-site and reuses the greywater during construction to reduce overall consumption.
Abbott also leverages partners to find new and improved tracking methods. “We are using the Contractor’s Commitment tracking template that a partner company showed us,” says Fait. “Each category has a field where project teams can provide feedback on how the goals were achieved—was it difficult, was there a cost impact, etc.”
WORKER WELLNESS
With increasing global attention to mental health and wellness and the encouragement of the Contractor’s Commitment, all four STOBG signatories have made jobsite wellness a priority. Each company has regular and frequent wellness breaks—whether educating teams to stretch and flex before work or promoting health habits such as taking a break or staying hydrated.
Ultimately, the impact of signing the Contractor’s Commitment illustrates how each business unit is working to consistently implement best practices—which reinforces our Quality 360º program, striving to deliver the highest quality in everything we do.
5 CATEGORIES OF THE CONTRACTOR”S COMMITMENT
Contractors who sign the Commitment pledge to meet a series of goals in five categories
- Carbon Reduction: How well a contractor reduce carbon emissions
- Jobsite Wellness: Fostering wellness (clean air, nourishment, mental health, etc.) for anyone working on-site or in jobsite offices
- Waste Management: Promoting waste diversion, whether seeking green building certification or not
- Water Management: Assessing risks to prevent water pollution
- Material Selection: Assessing and selecting healthy and sustainable materials
Originally Published in STOBG Insights Issue 2 2023.
As design trends come and go, law firms have historically stuck to a more traditional workplace aesthetic that is, in many cases, rooted in more than a century of legacy. However, with unprecedented challenges and shifts in workplace dynamics in the last several years, some trends are emerging.
“Our business really got started with law firms,” says Mallory Wall, project executive at BCCI Construction. “For the last 35+ years, we’ve delivered several law firm projects every year. Each law firm has its own unique needs and wants, but in that time, we’ve also seen some consistency across the sector, especially with all the uncertainty in the workplace since the pandemic.”
The big question? How to handle the return to the workplace since COVID. Many sectors have begun to adjust to a new, more flexible business model. The legal sector hasn’t quite settled on how to handle it.
“Other businesses are gearing their offices more toward creating spaces for employees to come in for collaborations and meetings only while they do their day-to-day work from home,” says Luke Thomas, director of operations at Structure Tone Philadelphia. “Law firms haven’t typically been as open to that kind of change, but we are starting to see it in their projects.”
One reason, says Wall, is the competition for talent. “Law firms are losing recruits as big tech firms hire them directly. Because we work with both tech firms and law firms, we’re able to offer some advice on what they can do to communicate a more modern vibe that’s most like that of a tech company.”
THE SHIFT
Even before the pandemic, law firms were starting to incorporate more café spaces and casual collaboration areas. With added pressure to convey an attractive culture, law firms are taking those amenities to a higher level.
As crazy as it sounds, says Wall, asking employees what they want can be the most effective means for attracting and keeping staff.
“Many of our clients have been torn between sticking with tradition or branching into more trendy workplace features. We suggest they survey their staff to ask what they think. They’re often shocked to find out it’s usually not about having ping pong tables or bean bag chairs, but things like nicer bathrooms or more lounge areas and break-out rooms. Those smaller upgrades can have a big impact on culture.”
Mallory Wall, BCCI Construction
THE LESSONS
As the companies within the STO Building Group have continued to help law firm clients navigate this paradigm shift in the workplace, it became obvious they could learn from and help each other. And so the organization’s law firm initiative was born.
Representatives from across STOBG’s 13 companies, including BCCI and Structure Tone, meet on a regular basis to discuss trends, share lessons learned, and connect the dots for clients looking to upgrade or build offices in other cities. For some clients, the benefits are already clear.
“We have a great relationship with Gunderson Dettmer,” says Wall. “When they mentioned they were going to start a project in Austin, Texas, we were able to recommend an architect, introduce them to our Structure Tone Southwest team, and stay involved and engaged throughout the project.”
The same goes for negotiating the mounting challenges of the supply chain. STO Building Group’s procurement experts track trends and issue a monthly report on which materials are experiencing supply chain delays and which may be easing. The entire STOBG network has been able to bring that intelligence to their project teams to help inform decision-making.
“The information a team in one city has been able to share with colleagues in other locations has undoubtedly benefited our clients’ processes,” say Eugene White, STO Building Group executive vice president and leader of the firm’s law firm initiative.
“From supply chain challenges to local market nuances, it’s been extremely helpful to have that level of expertise behind our local teams. Advancing lessons learned from one project to another has helped us ensure more predictable outcomes.”
Eugene White, STO Building Group
The efficiencies a client gains from working with this network of experts creates a win-win situation for everyone. “The client has a great experience, and we get to establish even stronger relationships with our sister companies,” says Wall. “Our clients tell us it’s just like working with the local team they know and love.”
THE FUTURE
Although the crystal ball does show a few changes in the future of law firm design and construction, law offices will undoubtedly continue to reflect legacy, reputation, and professionalism. The trick is finding just the right balance.
Gone are the days of the traditional law firm. We’re in a transition period, and culture will be key.”
Mallory Wall, BCCI Construction
Luke Thomas agrees. “I believe law firms will move into creating more amenity spaces for everyone and less hierarchy in terms of designing extravagant office for attorneys. The change will be slow, but they’re getting there.”
RECENT PROJECTS
BCCI Construction and Structure Tone Philadelphia have recently completed office projects for dozens of law firms, including these. (Bold indicates clients shared across the STOBG network.)
Akin Gump
Baker Hostetler
Blank Rome
Debevoise & Plimpton
DLA Piper
Faegre Drinker
Fish & Richardson
Fisher Phillips
Fox Rothschild
Gibbons
Greenberg Traurig
Gunderson Dettmer
Hogan Lovells
Kilpatrick Townsend & Stockton
Kirkland & Ellis
Morgan Lewis
Troutman Pepper
Originally Published in STOBG Insights Fall 2022
Eataly: A lively Italian marketplace with restaurants, food and beverage counters, a bakery, and more.
STO Building Group: A family of companies with a client-first mentality that keeps us at the leading edge of construction management. Two separate companies brought together by one common goal: to build amazing spaces.
2019 EATALY TORONTO
Govan Brown began their partnership with Eataly in 2015 after John Brown and Tom Mason met with partners from the global Italian marketplace looking to build in downtown Toronto. Challenges are inevitable in any construction project—especially such high-profile, high-finish projects like an Eataly Marketplace. Eataly Toronto was no exception. The three-story building, which opened in November of 2019, is Canada’s first Eataly location. Sitting at the corner of Bay and Bloor in the Manulife Center shopping mall, Eataly Toronto greets its guests with a street-level entrance and an interior crafted with two long passageways. The 50,000 sf building includes a new marketplace, a grocery store, and various bars and restaurants.
“Being able to have their trust and to deliver for them in many different markets with great teams is what I’m most proud of. It’s an amazing and rewarding experience, for sure.”
Tom Mason, Govan Brown
Eataly’s goal is to create an authentic Italian eating experience, so obtaining proprietary Italian equipment is vital. From custom-built wood-burning ovens and bakery equipment to high-end terrazzo flooring, many components are made in Italy and shipped to North America. However, equipment that is designed to European standards doesn’t always perform the same way in North America. The certification process for European equipment combined with the different infrastructure requirements made implementing these proprietary components a challenge. The project team had to work very closely with their European partners and local engineers and subcontractors to work through those conversions to make it work as if it were operating in Italy.
But all challenges come with lessons learned. After the Toronto project, the team prepared a presentation deck and walked through what worked and didn’t work with each STOBG business unit with potential Eataly projects ahead. “After every large project at Govan Brown, we do an after-action review,” says Tom Mason, account manager at Govan Brown. “We tried to be as detailed as possible and highlight many of the lessons learned on Eataly that the Structure Tone London, Southwest, and BCCI teams needed to incorporate to make their builds successful. We find that these sessions are beneficial to both client and construction manager.”
2020 EATALY DALLAS
When Structure Tone Southwest began talks with Eataly to take on their new Dallas, Texas location, the project team jumped into research mode. They met with Gensler, the project’s architect, as well as Eataly consultants to ensure the final construction drawings were approved. An additional meeting in New York soon followed to verify the value engineering efforts. “We had quite a bit of education during those meetings,” said Eduardo Linss, project manager at Structure Tone Southwest. “On the visit to New York, we visited their flagship store in the Flatiron District and got a real feel for the flow of the store.”
Eataly Dallas consists of three floors with the markets, various to-go counters, and a pizza and pasta restaurant located on the second floor and a high-end restaurant on the third. The building welcomes guests with street and mall entrances and gives a comfortable yet sophisticated atmosphere with wood seating inside the restaurant areas, including the Gran Bar, a full-service, Italian-themed coffee bar on the first floor.
“Going through the grand opening, to hear the Eataly team say this is the smoothest build they’ve had in Dallas was definitely something I took away with me. It spoke volumes to the level of execution of the team overall.”
Eduardo Linss, Structure Tone Southwest
As Govan Brown passed down their lessons learned, the project team was able to adhere to the level of expectations Eataly sets. Although each store in each market has its own standalone identity, it was important for the team to set a preliminary standard of execution for subcontractors. This ensured everyone was on the same page for the project and the client’s expectations from beginning to end. The Dallas team was able to use the Govan Brown team as a sounding board and talk through potentially challenging scenarios. In turn, Structure Tone Southwest was able to do the same for BCCI Construction. “Everything inside the marketplace has a unique look,” says Linss. “It was an intense project, but it was well organized.”
2021 EATALY LONDON
In London, Structure Tone began working on Eataly’s new location facing two completely different challenges than their peers: COVID-19 and Brexit. Despite the local challenges, the site stayed open throughout the early months of 2020 during the height of the COVID-19 pandemic. Brexit proved to be far more problematic during the early part of 2021 where travel and shipping restrictions made life more difficult. Despite the hardships, Nik Quarm, senior project manager at Structure Tone London, sees Eataly London as nothing short of a success, thanks in large part to the information sharing and resources across the STO Building Group team. “The key to successfully delivering Eataly’s first UK store was utilising the benefits gained from STOBG’s global partnership with Eataly,” he says.
“This was a program-driven exercise. Yes, quality is essential, but having a program partnership is just as important and, quite frankly, the key to delivering a project.”
Jack Dixon, Structure Tone London
As the winner of the 2021 Mix Interiors Bar and Leisure award, Structure Tone London and Eataly truly transformed the 42,000 sf building into a vibrant and engaging destination. Located next to Liverpool Street Station, Eataly London welcomed visitors to their grand opening in April of 2021. With colossal revolving entrance doors that lead to the Gran Bar, the London site includes two floors of pizza bars, grab-n-go foot markets, a towering indoor bar area, and an outdoor terrace. The market also offers a variety of quality Italian food products and houses London’s largest Italian wine cellar. “I’m proud of how my team communicated with Eataly, especially with the different cultures, languages, and currencies,” says Jack Dixon, project director at Structure Tone London. “We delivered this project through such difficult times, and I’m especially proud of how Eataly trusted us throughout to deliver a great project.”
2022 EATALY SILICON VALLEY
In North America, Eataly continues to expand with a new location on the West Coast. BCCI is currently bringing the Italian marketplace to Silicon Valley’s Westfield Valley Fair Mall in San Jose, California. Like its sister stores, the space will offer a mix of restaurants, cafés, bars, and to-go counters. After visiting several of the Eataly North America locations, BCCI also went through several lessons learned sessions with both Govan Brown and Structure Tone Southwest. “We went through the project insights they complied on preconstruction and issues they faced with specific subcontractors and processes during the build,” says Dave Herskowitz, senior program director of integrated services at BCCI. “What we learned allowed us to build a schedule and a more informed budget and discuss how to avoid similar challenges with the client.”
“The fact that Govan Brown built in Toronto and Structure Tone Southwest in Dallas gave Eataly confidence to partner with BCCI on the Silicon Valley location and the certainty we would deliver the same level of service in terms of execution, responsiveness, and quality.”
Dave Herskowitz, BCCI Construction
Now three months into construction, BCCI has collaborated with Govan Brown and Structure Tone Southwest frequently to help troubleshoot and think through challenges. “We’ll check in with Govan Brown and Structure Tone Southwest and ask how they solved similar challenges,” says Herskowitz. “I’m also proud of the general willingness and enthusiasm from both teams. They immediately answer whenever we ask a question. They’re happy to jump on a call. It’s amazing to have that level of support and collaboration.”
Herskowitz is also excited about the prospect of supporting Eataly as they begin budgeting and reviewing other Eataly locations on the West Coast. “The collective experience of building the North American Eataly stores is helping shape program strategies for Eataly which can be applied to future builds.”
Originally Published in STOBG Insights Fall 2021
In January 2020, a cutting-edge automotive technology company—joined by AP+I Design and BCCI Construction—kicked off construction to transform a 111,000 sf building into their new headquarters. Then, a global pandemic and record-breaking wildfires threatened to throw the entire project off course.
Located in the heart of Silicon Valley, Mountain View, California is an ideal location for a growing tech company’s offices. Now completed, the open plan features plenty of amenities, including conference
and huddle rooms, break areas, gender-neutral bathrooms, wellness rooms, a fitness center and game room, plus a 5,000 sf full-service café and large dining area. Accompanying the administrative areas is an
8,500 sf automotive shop and 11,700 sf of R&D lab space.
The layout is split into four, landscape-themed quadrants—you’ll know whether you’re in the lake, beach, desert, or forest building by the whimsical wayfinding wall graphics and signage, and creative conference room names. And the attention to detail doesn’t stop there—the client and design team selected lighting that mimics highway delineation lines for the ceiling and placed crosswalk graphics on the floor to reflect the company’s mission. There’s even a section of the building the client refers to as “The Open Road,” which is a wide circulation area featuring high, suspended ceilings. “It was specifically designed to be wide enough for the client’s car models,” says Katherine Schurba, BCCI project manager. “So, if they wanted to drive a car through the building, they could.”
BUMPS IN THE ROAD
Like most projects that kicked off in 2020, this build-out didn’t exactly go to plan. From manpower issues to scope clarity, the team faced several unforeseen logistical challenges during construction that could have impacted the quality of the end result.
Scope. While the headquarters build-out was underway, the landlord was upgrading the 1980s building and utilities. When BCCI was onboarded, the team realized the landlord general contractor’s design didn’t match up with their plans. Elements like the placement of storefront doors and skylights were either slightly off or missing altogether. Once the plans were reconciled and each contractor’s scope clearly outlined, the next challenge was managing the logistics—and relationships—between the landlord GC’s team and BCCI’s. “We made sure that everyone understood where our scope stopped and where the other contractor’s scope started,” Schurba says. “This continual communication helped us maintain a respectful atmosphere on-site.”
Schedule. The project’s progress was interrupted by COVID-19 and the region’s shelter-in-place orders last year. Once they were able to return to the jobsite, BCCI’s team and their subcontractor partners had to become experts in demobilization and remobilization. If a suspected COVID-19 case was reported, the jobsite was shut down, sterilized, and tested by a hygienist. Despite the effort to sanitize the space, getting a full crew, or the same crew members who were familiar with the project, back to work the next day was a challenge. BCCI worked closely with the foremen on these labor obstacles and staggered shifts to keep the project on track.
Power. The project also required a power service upgrade by Pacific Gas and Electric Company (PG&E). Due to the wildfires, these types of upgrades were postponed considerably. The project’s scheduled delivery date was December 3rd, and as the project progressed, it became increasingly clear the power upgrade wouldn’t be completed in time. In order to stay on schedule, BCCI continued to build using generator power. Understanding this delay was out of BCCI’s control, the client agreed to accept their finished space without any of the permanent power related elements. “I have never built an entire space from start to finish without permanent power,” says Matt Ludwig, BCCI superintendent.
A QUALITY FOUNDATION
Each of these extraordinary challenges makes BCCI’s on-time delivery and zero punch at move-in all the more impressive. To the team, the project’s success was a result of BCCI’s unique culture of quality.
From their robust quality control training program to a detailed pre-punch process, quality is engrained in BCCI’s project planning and implementation. In fact, many of their field and operations staff—including project superintendent Matt Ludwig—started their careers at BCCI in the quality control program, where they were trained to analyze drawings, identify potential quality and scope issues, manage relationships with subcontractors, and support project teams on-site.
“A lot people think of quality control as a static role—a position you need to fill—but at BCCI, it has a long history of being a springboard position. You have to master the details to be able to scale your success and grow your career.”
Lisa Dunmeyer, Studio Director & Quality Manager, BCCI Construction
On this specific project, BCCI quality control coordinator Eric Aboytes, who is currently in the training
program, arrived on-site a month before delivery to assist the project team and begin a pre-punch process. Without power, Aboytes swept through the project with a battery-powered work lamp and noted deficiencies and quality of workmanship—each of which was closed prior to delivery in December.
When the space finally received power in February, Aboytes did another sweep to make sure the finishes were up to BCCI’s high standards. “Obviously, with the lights on you can spot imperfections so much easier,” Aboytes says. After his final pass, the architectural punch walk resulted in only 75 items for the 111,000 sf space and all were resolved prior to the client’s move-in a week later.
According to Dunmeyer, this project’s positive outcome is yet another example of BCCI’s top-tier quality program at work.
“Even when you have challenges that are outside of your control, with a quality program like this, you can problem-solve as a team,” Dunmeyer says. “BCCI’s quality program builds teams that come together, solve for adversity, and deliver to the highest standards.”
Check out the podcast Quality Construction: A Celebration of Workmanship to learn more from the project team about the quality control process for this headquarters build-out.
In the modern era of sustainable building, human health and well-being continue to be at the forefront. The WELL Building Standard remains the leading tool for upgrading the physical environment of a building through improvements to air, water, light, acoustics, and other factors. Now more than ever, companies are looking to the design and construction industry to help enhance the occupant experience, whether pursuing the WELL Building Standard for the first time or preparing to recertify their space.
For businesses that have attained WELL certification, the recertification process enables them to renew their commit to health and wellness in their policies and the operation of their built environment. Once a company’s space is WELL certified, it must recertify after three years to ensure it continues to meet the rigorous standards and optimizes occupant health and productivity. But what happens if the rating system updates to a newer version or the goals of the organization shift? BCCI Construction’s Professional Service team weighs in on that question and shares tips to prepare for recertification.
Determine your goal. According to BCCI director of sustainability, wellness, & ESG Kena David, there is an advantage to upgrading to a newer version if a company wishes to pursue a higher certification level. For instance, “WELL v2 allows for more flexibility and offers more optimizations to aid in the pursuit of obtaining Gold certification if a company is currently at the WELL v1 Silver level,” she says.
Document annual maintenance and service. Regardless of whether a company decides to upgrade, the first step is to make sure yearly reporting is complete. This includes mechanical maintenance, janitorial maintenance, and occupant surveys. “We tend to check in with our clients who have just achieved certification and ask if they liked our help with annual maintenance and reporting services,” says David. “We want to make sure they’re prepared every step of the way.”
Plan ahead. When the decision has been made to reapply for WELL v1 or to upgrade to v2, gather all documentation, along with any annual reporting, policy and design changes, and performance testing completed within at least 6 to 12 months before enrolling for recertification. “A month or two before that three-year mark is when a company should get re-engaged to assess what needs to be updated,” says David. “Then we can correspond with the review team and get the on-site testing to happen within about six months of their timeframe, which would be ideal.”
Check what’s new. COVID-19 undoubtedly influenced how we maintain our spaces, especially in communal areas and regarding indoor air quality. Some of the COVID response has benefited WELL projects with air quality now monitored more closely, as mechanical and building engineers maintain better records and have increased filtration and frequency of cleaning. Other aspects of the COVID response that have changed operations are substituting fresh fruits, vegetables, and salad bars with prepackaged, processed foods to avoid potential viral contamination. Before recertifying, project teams should assess these types of policy changes that may affect their company’s WELL recertification.
Communicate and coordinate. In the event that policies have changed or the physical space has been renovated, David says that defining a schedule for quarterly check-ins is critical to staying on track with WELL recertification. Reengaging with your WELL consultant also helps keep the recertification process organized and efficient.
Consider cost. Lastly, project teams should consider the cost of recertification, particularly if there might have been alterations to the space or building that will affect the cost of recertification. According to David, the project team or WELL consultant should have a good line of sight to the budgetary implications and understand the client’s fiscal year. That way they know the best time to have the budget conversation and make sure there are no surprises down the line.
“One of the unique benefits of the work we’ve been doing with the recertification process is our continued relationships with our clients,” says David. “BCCI’s Professional Services Group continues to be the go-to for clients looking to pursue their recertification, not just the initial certification when they’re going through a build.”
Halie Colbourne, Sustainability Associate and Matthew Koester, Sustainability Coordinator | BCCI Construction
This year, BCCI’s Sustainability Team had the privilege of participating in the U.S. Green Building Council’s GreenerBuilder Conference, San Francisco’s premier venue for architects, contractors, owners and other green building professionals to learn about cutting edge projects and latest trends in the Bay Area.
The conference opened with Vien Truong, CEO of The Dream Corps, who led the opening plenary. The Dream Corps champions nationwide policy to advocate for and address the needs of disadvantaged communities. Truong wove several threads, including the effects of poor air and water quality on Oakland and Flint-raised children, renewable energy, and state policy into a moral imperative for green building. In building inclusively and designing to mitigate the impacts on water and air quality, Truong notes that we have an opportunity to lift up disenfranchised communities and employ the community in a green economy. This theme was carried throughout the rest of the conference.
The first session focused on Rebuilding Resiliency, a crucial topic in the Bay Area due to the devastating wildfires that seem to occur during any season in California now. Led by Ann Edminster (Design AVEnues), Robin Stephani (8th Wave) and Bob Massaro (Health Buildings) the panelists shared solutions such as the urgency for cities to develop temporary housing ordinances. The idea is to utilize prefabricated housing for temporary use during and after natural disasters, similar to what Homes for Sonoma has been doing since the massive wildfires erupted in the North Bay last October. The speaker’s firms are actively working towards connecting wildfire victims with tax credits and rebates to rebuild their homes with features including Energy Star appliances, solar panels and passive heating and cooling systems. Massaro said Healthy Building’s projects are moving away from using natural gas as this can cause dangerous flare ups in the aftermath of these wildfires. He further explains that when building for a homeowner, his firm analyzes their fire insurance policy to pressure the company to finance these measures. The panelists also noted that the wildfires can still impact buildings throughout the Bay Area with high levels of particulate matter. Indoor air quality is a major component of LEED and WELL projects, and smoke/particulate matter (PM) levels become a concern when most building systems have to accommodate a minimum level of outside air. It is important to realize that wildfires directly impacting residential homes in Northern California can also indirectly impact commercial buildings in the city. Focusing on resilient building practices supports the green economy and reinforces the triple bottom line: people, planet and profit.
The session Women in Green: The Power of Diversity was another wonderful session led by Gabrielle Bullock (Perkins+Will), Kimberley Lewis (USGBC) and Andrea Traber (Integral Group) who highlighted the importance of diversity and inclusion in the workplace. Bullock began Perkins&Will’s Diversity + Inclusion + Engagement council in 2014 as a way to foster their culture’s talent and engagement, and to create a “diverse and inclusive practice and profession”. Bullock shared some of their focus areas such as recruitment, retention and mitigating unconscious biases. At the onset of this council, they measured their workforce gender balance, finding that women in leadership make up 25 percent where the AIA (American Institute of Architects) industry average is a mere 17 percent; in 2014, 44 percent of their workforce was comprised of women. Through their devotion to diversity and inclusion they have managed to increase their percentage to 48 percent women in the span of four years.
Their commitment to workplace diversity has produced impressive project wins as their clients are looking for diversity in a project team. Traber elaborated on these metrics mentioning the International Living Future Institute’s JUST Label which has helped Integral Group quantify similar metrics around gender equality and transparency. As a participant of the JUST Label, we were pleased to hear other companies using the JUST Label as a metric. BCCI committed to its JUST Label in 2014 and since becoming a JUST company has been able to benchmark, create and improve existing policies, as well as utilize the platform to increase our company transparency. The JUST Label allows companies to understand where there might be room for improvement. BCCI is currently working on obtaining better data in the Equity category as a commitment to one of our core values, Transparency, and to continue to strive for authenticity and equality in the workplace.
As Kimberly Lewis, USGBC’s Senior Vice President stated, progress towards a green economy has not been without its moral challenges. From building resiliency for natural disasters to increasing equity in the workplace, we are excited to see these challenges being addressed by visionaries like Truong and our green building community. In Truong’s words, we will continue to “build up, build power and build the future.”
As COVID-19 cases in the US continued to climb earlier this year, construction firms in hot spots like New York City knew it was only a matter of time before jobsites were shut down. But for some contractors, that call came much earlier than others. On March 16th, Boston and the San Francisco Bay Area became the first regions to issue shelter-in-place orders and shut down construction activity—so what was it like to go first? Mike Ryan, SVP of Structure Tone Boston, and Michael Fraley, VP of field operations at BCCI Construction, discuss some of the challenges they faced.
What was it like to be in that first group of cities to shut down construction activity?
Fraley: The most significant challenge was the uncertainty of the situation. There was no best practice or frame of reference to guide our actions, policies, and procedures. In the beginning, state and local officials were not coordinated and often issued conflicting orders, which made the situation even more challenging to maneuver.
Ryan: Yes, this was all new to us. Our top priority was the safety of our employees and the safety of our jobsites.
How did you begin shutting down sites quickly but safely?
Ryan: We created site-specific checklists with key items to tick off before closing each jobsite—things like removing trash, organizing work and supply areas, shutting off any valves, and locking electrical panels. Before exiting, we did final walk-throughs with the building engineers to make sure each site’s systems were off.
Fraley: We assembled an internal team to develop our demobilization approach. The group discussed and combined different ideas to create a comprehensive plan with easy-to-follow checklists, which we shared with building management teams. In some cases, BCCI’s plans and checklists were even used to assist with the shutdown of non-BCCI project sites.
What were you able to work on during the shutdowns?
Ryan: From continuing to pursue work to creating back-to-work plans, we were very busy during the shutdown. I led Boston’s “Return-to-Work” committee, and we jumped right into drafting those plans. We were constantly asking ourselves the “what-ifs” and really trying to come up with measures that would make our employees feel welcome in the office and make sure subcontractors and our own people felt safe on-site.
Fraley: I agree, there was quite a lot to do during the shutdown. While our preconstruction and project management teams kept in touch with clients, our field staff was busy drafting demobilization checklists, master schedules, and three-week lookaheads to prepare for remobilization.
As other cities began ceasing construction activity, and as you began gearing up to return to jobsites, what lessons learned were you able to share?
Fraley: Being one of the first to cease construction and then remobilize, we’ve had the opportunity to share a number of lessons with other STO business units. We remobilized over 20 projects, which required precise scheduling to accommodate a large number of deliveries over a very limited timeframe. We pre-stocked items in our warehouse to facilitate the rapid reloading of the delivery trucks. The first deliveries began at 12:01am on the official reopening day and continued around the clock until each project was complete. This approach helped us get our projects back online quickly and was shared with the rest of STOBG.
Ryan: As other cities began to shut down, we shared our expertise, and vice versa. When Boston started getting ready to head back to the field and the workplace, we were able to leverage the experiences of our colleagues in different locations who had continued operating. I think one of the positives that has come out of this situation is we’ve really come together as an organization to help one another through each stage of this COVID-19 rollercoaster.
How do you see COVID-19 impacting our industry?
Fraley: Our teams have done an excellent job developing strategies to respond to the ever-changing governmental orders and public health recommendations. As we continue to move through this evolving situation, planning has never been more paramount, and we’re translating what we’ve learned so far into an overall BCCI business continuity and disaster recovery plan.
Ryan: Initially, construction is going to be slower to allow for extra spacing on jobsites, additional shifts, and staggered site entry and exit. However, some clients still haven’t returned to their buildings—meaning we can work more efficiently without the noise and dust restrictions of an occupied space. In the longer term, I think this situation has forced us to slow down. In construction, we’re constantly pushing forward to get the job done, but now we’re looking at each situation and project from a different perspective and I think that will lead to innovations down the road.
Picture this: Recycled materials, paper, plastic, and even hair, shaped into a brilliant piece of art in the middle of an office. This incredible vision was created by WRAP, the Waste Reduction Art Project, to stop the cycle of building waste. Founder Yana Good Nigen established the project in February 2020, along with several talented artists, to help the world live more sustainably and positively impact the environment. BCCI Construction’s Mallory Wall is a member of WRAP’s advisory board and joined Nigen to discuss how WRAP makes a difference.
How did you get involved in WRAP?
Nigen: During my career in human resources, I saw disconnects between the departments that take on corporate social responsibility versus the execution level of HR and employee engagement. Coming from a background in both HR and marketing, I was able to navigate that space and bring the idea of recycling as fun and creative to the corporate culture. My thought process began with making recycling a priority for leaders and giving them the tools and know-how to implement that process into their organizations.

Wall: I learned about WRAP through a client, and she introduced Yana to me, virtually. BCCI is very big on sustainability. In construction, we tend to produce a considerable amount of waste and BCCI’s involvement with WRAP helps us understand how we can make a difference and a positive impact on our environment. Our effort is about getting the message out there and understanding waste and how waste can make art. It’s important to socialize these things internally and externally, utilizing some of our existing relationships with architects, designers, and clients. We want to continue to message anything that allows us to think outside of the box. This is one of many little things that can make a difference…and the artwork is beautiful, fun, and creative.
Nigen: I can’t thank Mallory enough for being such an advocate for WRAP. I absolutely appreciate everything Mallory does as a member of the board.
How do you find artists?
Nigen: I started calling and networking with artists I knew were great matches for WRAP. Everyone thought it was a great idea to bring in artists to get corporate clients excited about saving the planet in a fun, creative way. Our artists have such rich stories about the way they collect their art. One walks around his neighborhood in Amsterdam and collects pieces, creates sculptures, and places them throughout the community. Another creates incredible tapestries out of hair. We’re currently working on adding new artists to create that global footprint.
What does WRAP offer to companies?
Nigen: WRAP began with the idea of going into corporate offices and doing work within multiple locations. Unfortunately, COVID-19 has set us back from physically going into the offices and building art pieces. Our solution was to create virtual workshops, which we’re continuing. In fact, we hosted a virtual workshop with Zillow’s employees that was very successful. Ten thousand employees of the company participated, and they were able to create recycled art pieces with guidance from our WRAP artists.
But we began with several different services, such as office augmentations in terms of furniture and design. For example, we spoke to a client with several cabinets and other furniture that they were discarding. They asked our artists if they could make something fun and creative out of these objects. From there, our artists planned and designed those specific pieces for said office. Thus, the history of how the office grew and evolved is captured in that art piece and the discarded furniture did not go into landfills.
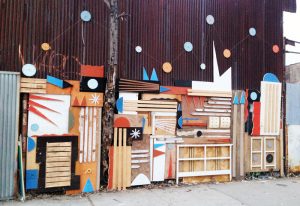
We use artwork for both corporate social responsibility and environmental, social, and governance (ESG) reporting. WRAP artists can bring in recycled art to make the reports come alive and showcase a report’s graphics. We also have employee engagement events, host corporate mural festivals, and can create company gifts made by WRAP artists.
WRAP also measures impact. We partnered with Empower, a global company based in Europe, that applies the blockchain idea to track the collection and assemblage of art pieces. For example, we host an employee engagement program at a company, and every employee contributes a portion of recycled material. Later, all these pieces are sent to the artists, and we track the entire history. It’s completely anonymous and by department. Not only is it accurate and visual, but the companies always enjoy it.
What do you enjoy most about working with WRAP?
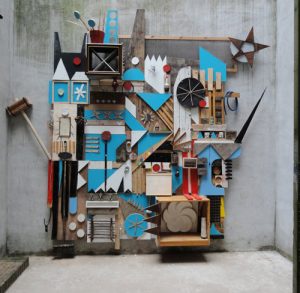
Wall: I like the idea that we’re a team. We’re all learning to explore creative ways in which we can transform waste into something beautiful and make a positive impact. There is so much opportunity with our network of relationships, from architects and designers to owners and clients, to think outside the box and create installations for companies and public spaces that can be appreciated.
Nigen: I am so proud of the WRAP team. They’ve persevered through COVID-19, helped keep WRAP going, and continued with the virtual workshop. I’m also proud of our WRAP artists who continue to build and create art in such difficult conditions. However, we’re ready to bring in our artists to collaborate with companies and host additional mural festivals.
What’s next for WRAP?
Nigen: Our immediate plan is to get more artists on board. We’re constantly adding new artists and getting in front of as many clients as we can to bring this idea to corporate culture. We’re looking at growing an educational component where we would provide services to low-income communities, whether schools or senior living facilities, on how to create recycled art. We also value our relationship with BCCI and look forward to working more together!